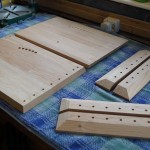
Bridge tops and feet are now planed up, and essentially complete bar sanding and finishing. I decided to bevel all edges of the bridge tops to the same angle as the baffle support bases for the sake of design continuity.

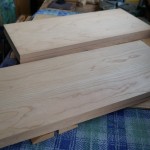
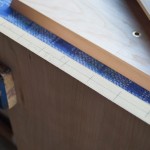
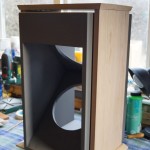
Planing the cross grain on the bridge tops required the usual degree of care to prevent end grain splitting – I purposely left 3/8″ of waste along the back edge and planed the sides from front to back before trimming this back to the line. Whilst bevelling the edges I also used my trusty aluminium clamps across the work to further support the end grain. The photos show all finished hardwood elements (one bridge top is upside down) with feet detail, dowel holes drilled.
Time to start on the veneered side panels. These were supplied by SL Hardwoods with an “A” and “B” side; the grain on the “A” side has interesting swirls, and I am looking forward to seeing how these come up with the oil. Following the marking out and drilling of the dowel holes in the four sides I was able to do a trial assembly of the bridges over their woofer boxes. All fitted well and looks great. You can see the slight bow on the bridge tops – the clamps will sort that when glueing up. I am planning to glue the bridge parts using the woofer boxes as jigs / guides to ensure the side gaps and angles are true. Regrettably, much sanding is ahead before then!