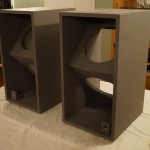
The woofer boxes had their second full primer coat several weeks ago now; it was with a mixture of relief and apprehension that I picked up where I had left off with them – relief that the end of the project was in sight, but apprehension about achieving a reasonable quality finish – especially round the corners of the front / top. That stubborn end grain persists in showing through despite much sanding already.

First thing was to set up shop with dust sheets etc in the music room; temperatures have plummeted to -4 deg C overnight in the last few days. Woofer boxes and paint now ensconced indoors – WAF surprisingly compliant. I was planning to give the boxes an initial coat of matt black to assess finish to date, and almost forgot that I hadn’t made the Speakon brackets! Back out to the garage, well layered up… Quick job though – pics show these in place. Again, I am not gluing these to make wiring up easier later.

On with the matt black – and they look really good. However on closer inspection the problems with visible joints and end grain around the top front flap remain considerable, especially the box on the right in the pic. The flash photography is merciless here, and makes the problem look even worse than is apparent in real life. At this point one voice in my head was telling me “no-one will notice – get the woofers in!” whilst the other (OCD) voice said “you’ve got this far – a few more days is a small price to pay…”.
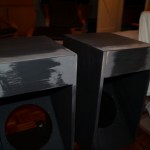
It was a close thing, but the OCD came out on top, and a radical sandpaper attack on the top fronts followed. To get the joint lines clean I had to go back down to bare wood in places. Stress. It also meant lugging the boxes repeatedly between house and garage for the sanding. Back to the primer, and three coats later (fine sanding between coats) one box was good – I now cannot see any wood grain even in strong light. The other box however is putting up more of a fight, and despite another coat and sand the end grain STILL keeps popping up. So back to the filler again… hopefully after a gentle sand-off tomorrow and yet more primer it will capitulate. The back corners can look after themselves however – the OCD lost this one!
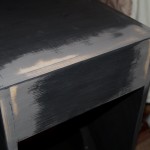
I took several more photos of this miserable process, but, you know, they are so boring, so I am sparing my readers…
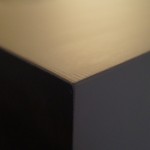
After a further sand down and more primer, this looked practically the same!
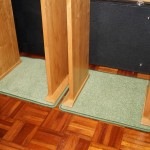
Whilst all this was going on I had been mulling over floor protection, and remembered we had some small rolls of carpet offcuts. Better still, I discovered a local carpet edging company only 15 mins away (had thought about, er, learning another skill, but some quick research made it clear that acquiring the necessary kit would cost a lot more than their charges). I now have two custom mini-rugs for my speakers!